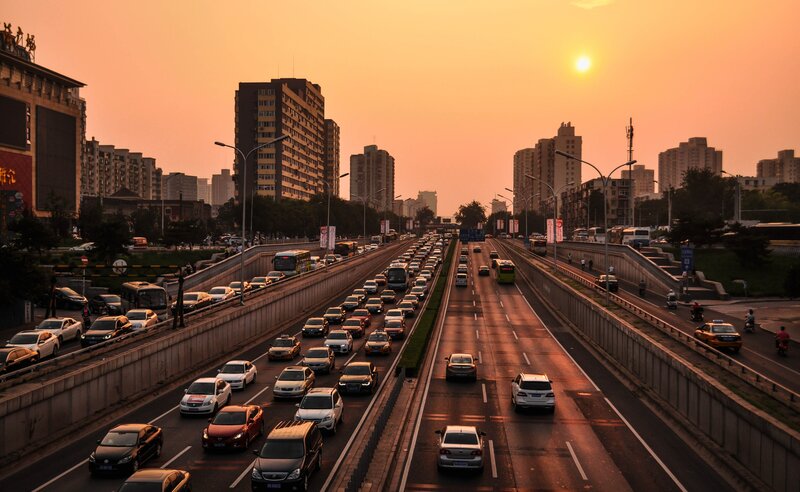
7 Tools for Identifying Operational Friction
What is operational friction?
Operational friction is one of the prime causes behind business failure. It’s the gap between the actual performance of a business in relation to its ideal operating conditions. All organizations experience the effects of operational friction at some point, as they work toward achieving their goals.
Here are 7 tools that help you find the origin of friction in your business or process and suggest methods to improve its efficiency:
1. Identify the primary sources of friction
Friction causes companies to innovate less often and drive costs up. Primary sources of operational friction include systems, people, policies, and attitudes that block or slow down innovation. An Ohio State study found that ‘in an 8-hour day, the average employee is productive for 2 hours and 53 minutes’. The rest of their day is lost to friction.
Identification of the sources of operational friction allows organizations to prioritize activities that will reduce friction and shift costs away from current activities that don’t drive value for your customers.
2. Choose a metric that matters
Find a way to measure the friction of your choice. Is the process difficult? Does the outcome seem random? Are there competing values? Determine a metric that will enable you to make decisions with confidence. The more information you have about your options, the less likely you are to make bad decisions.
3. Collect data with the right tools
Data collection is one of the hardest things to do well, but once you have it in hand, a lot of the hard work is already done. You just need the right tools to apply the data in the right way, and the best data collection tools do exactly that. That should ultimately be your goal when choosing a friction collecting tool.
4. Get a baseline value for your measurements
Establishing a baseline Friction value allows you to size the total potential improvement opportunity, and provides the ability to create an overall cost/benefit analysis based on the resource and technology spend required to improve.
5. Crowd-source friction discovery, quantification and removal
Make your staff part of the solution — they are the folks encountering friction each and every day, so it just makes sense to go straight to the source. All too often when aiming for productivity improvements, employees are viewed as the problem and not the solution. Wouldn’t it be more motivating and sustainable if your workforce played an active (but small) role in reducing friction?
5. Execute
Implementing the improvement is as important as making it. Once you’ve determined your desired outcomes, create a roadmap that breaks down the implementation into incremental milestones. Make sure you allow critical items such as employee training and UAT; and ensure you have a good understanding of the current workload conditions (peak volume period) and risks (eg. customer experience).
6. Measure and monitor progress
A good set of tools will help you keep track of any improvement initiative, providing metrics and visibility into both present conditions and expected results, at each stage of the implementation. Without this visibility, it becomes difficult to quantify the impact of the change, be it positive or negative, against the baseline.
7. Repeat the process
At this stage, if you’ve completed the process as laid out above, you’ll have objective data indicating the level of success the improvement initiative has yielded, and whether or not you’ve achieved the desired outcomes. The more you follow this process, the more you’ll see new areas of improvement emerge.
For high performing organizations, improvement isn’t just about getting better results in one area, improving one process, or solving one problem — it’s about constantly striving for continuous incremental improvements over long periods of time. There’s no doubt that it can take time to embed a continuous improvement culture, but putting the right tools and process in place is a pretty good place to start.